Ohio’s businesses were all for mask mandates. Then politics got in the way.
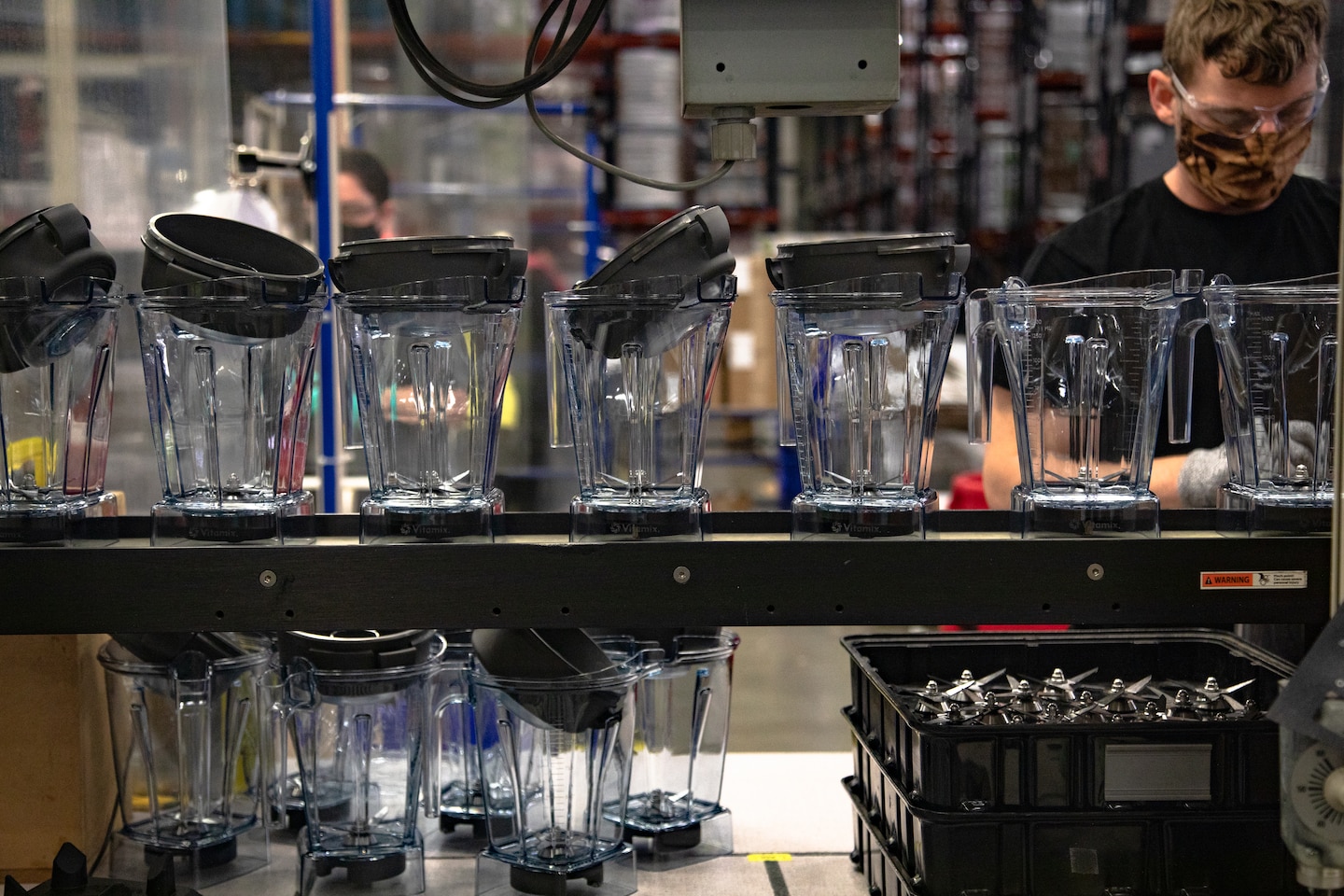
“After seeing all the shutdowns happening in China, I knew it would only be a matter of time before the virus got here, Berg said.
By late January, Berg had shifted work to the United States from a company in China making machine components used for production in her Strongsville, Ohio, plant. By early March, she was rallying management to devise what amounted to a “zero-infection” strategy for the facility. In mid-March, Berg joined other manufacturers in successfully lobbying Ohio’s governor, Mike DeWine (R), to keep factories open during the stay-at-home order, arguing industry had already come up with ways to prevent the spread of the coronavirus. And in April, an advisory board of business leaders appointed by the governor recommended Ohio adopt a statewide mask mandate and other measures.
The intervention was partially successful. In April, DeWine briefly ordered Ohioans to mask up in public before reversing the mandate in the face of public protests.
The governor renewed his mandate for face coverings in public on Wednesday, after the state experienced a spike in coronavirus cases and as Republican governors in other states introduced mask orders. About half of all states now require face masks outside the home.
But political and business leaders say those efforts by the business community helped Ohio contain the coronavirus in the early months of the pandemic, and kept factories operating without experiencing the widespread outbreaks in industrial facilities that have occurred in the meatpacking and other industries.
And it could help Ohio avoid the big spikes in infection that occurred after reopening in states like Arizona, Florida and Texas.
“You have a group of people who are smart and who have months of experience in places like Italy and Wuhan [China], where the virus was raging,” Jon Husted, Ohio’s lieutenant governor, said in an interview. “These are production facilities that didn’t have a single case of coronavirus because everybody wore a mask.”
At the Vitamix facility, a low-slung, tan building common to many suburban industrial parks in Ohio, the long hallway off the parking lot is lined with entries in a poster contest, on coronavirus prevention themes, for the children of employees. “If you get kids involved, parents look at things differently,” said Beryl Blaylock, the manufacturing manager. “When the kid comes home and says, ‘Daddy, why don’t you have your mask on?’ then it hits home.”
Until the coronavirus struck and shut down restaurants, Vitamix focused on commercial blenders, a favorite of professional chefs. For its health-conscious following, the blender held rock star status for its ability to do everything from whipping up smoothies to grinding nuts.
Berg is the fourth generation of her family to head the privately owned firm, headquartered in Olmsted Township, Ohio. It has more than 800 employees, including 300 at its Strongsville plant.
During the pandemic, with people cooking more at home, sales for the consumer line have increased, Berg said. The company is hiring additional workers to meet demand.
The work on face coverings started early in the pandemic. By March 9, when Ohio had its first confirmed case of the coronavirus, Charlie Gallagher, vice president of supply chain and operations, was already focused on stocking up on masks.
Ohio has a large auto manufacturing sector and because of globalization, relies on China for parts and increasingly for customers. Many of those auto plants in China are in Wuhan.
Ohio manufacturers with operations in China had been sharing with colleagues how masks had stopped the spread of coronavirus, even at facilities with thousands of workers. But there were shortages of industrially made masks, as well as cloth masks.
So Gallagher asked a neighbor, who has a small sewing business, if she could make masks for the plant. She could make 300 at $7 each. There was one issue. The only way she could fill the order was by using green-and-white material with a 4-H emblem.
“I said, ‘I don’t care what they look like as long as they keep people safe,’” Gallagher said. And so by the end of March, the plant was fully masked up. About a month later, the company was able to buy commercially made masks.
The plant, which has remained open throughout the pandemic, has had no recorded cases of coronavirus infection occurring at the facility, the company said.
Similar lessons learned from Ohio manufacturers with operations in China allowed the state to get an early jump on fighting the coronavirus, manufacturing leaders say.
Since more of Ohio’s businesses gradually began reopening in May, the state has seen a jump in known coronavirus cases. Ohio recorded a 11 percent increase in new coronavirus infections over the last week, according to Washington Post data. But the state has not experienced the dramatic surges of Florida and Texas, and Ohio still lags neighboring Michigan and Pennsylvania for total cases, adjusted for population.
And there have been no reported cases of widespread outbreaks at production facilities — such as those that tore through meatpacking plants in Iowa, Nebraska and South Dakota.
“If we had to replay this, we’d make different decisions,” DeWine said Wednesday, announcing the mask mandate. “Hindsight is always better.”
The governor had started off on a different direction in the spring, under prodding from prominent business interests.
Ohio was ahead of many Republican states when the DeWine administration’s stay-at-home order took effect March 23.
In April, the Governor’s Economic Advisory Board, led by a prominent manufacturer in the Cleveland area, put forward a number of recommendations for keeping industries in the state thrumming through the pandemic.
At the top of the list was a “No mask, no work, no service, no exception” policy for customers and clients, as well as their own employees.
Other recommendations included social distancing protocols, enhanced cleaning and sanitization of surfaces, and daily health checks, such as taking temperature of employees and visitors.
The board developed the stringent measures in part after watching how other companies’ globalized supply chains dealt with the virus.
And DeWine took note, adopting the measures on April 27, and issuing a statewide mask requirement for manufacturers and retailers — including in-store customers.
The move put DeWine ahead of many Republican and Democratic governors at the time.
The backlash was immediate. It was “pretty fierce and pretty quick,” said Frank Sullivan, chair of the advisory board and CEO of RPM International Inc. The company, which makes high-performance coatings, sealants and specialty chemicals, has 130 manufacturing facilities in 26 countries, including Italy and those in Asia.
Protesters claimed the masking requirement trampled on their individual freedoms. The political nature of the anti-mask movement baffled Sullivan. “I am a free-market, small-government conservative,” he said. “This isn’t about some in-your-face constitutional issue. It’s about doing the right health protocols to mitigate the spread and to keep Ohio’s economy going.”
A day later, DeWine downgraded the mask mandate to a recommendation. He also moved to start reopening the state, amid public debate that it was too soon.
“It was a wake-up call for our group,” Sullivan said. “I think we did a really good job of canvassing Ohio’s business community, but the governor of Ohio is the governor of everyone in Ohio, not just the business people.”
Husted blamed the backlash on Ohio being ahead of the times.
“I was concerned that the public wasn’t there yet,” Husted said. “It [being required to wear a mask] was brand new in America, a country that prides itself on individualism and personal liberty. I knew we needed a couple of months yet in educating the public on these things and bringing them along.”
Businesses were still required to have employees follow protocols such as frequent hand-washing and social distancing. Many manufacturers urged employees to continue such measures when they were off the clock, modeling them for family and friends.
Ethan Karp, president and CEO of Magnet, or Manufacturing Advocacy & Growth Network, in Cleveland, said companies realized quickly they had to pool information to keep up with a fast-moving situation.
“We wanted to be like a lighthouse for our industry and the economy — shining a light on the information manufacturers needed to navigate covid-19 and keep their people safe,” he said.
“The stakes were incredibly high,” he said. “Things were changing hourly and a lot of ideas were flying around. We realized we had to become instant experts on all things covid-19 to give manufacturers the practical information they needed to keep their people and plants safe.”
At the same time, industry members continued to work their contacts with the DeWine administration to try to apply those policies across the state, said Eric Burkland, president of the Ohio Manufacturers’ Association
“The DeWine administration has a deeply collaborative leadership style,” Burkland said. “This allowed us to engage industry subject matter experts in identifying safety and health best practices in the design of state policy. The result was, we think, the best policies in the country.”
Despite the protests, by early July DeWine had instituted a mask mandate for parts of Ohio, ranking each of the 88 counties according to the infection risk. Even before Wednesday’s statewide mask mandate, about 60 percent of Ohioans were under orders to wear masks outside the home.
For Berg of Vitamix, taking the lead on developing containment protocols for coronavirus seemed natural.
Manufacturers were already challenged to find workers, with fewer younger people attracted to the industry, even as the increased use of technology raised the skill level for entry-level jobs.
“We got a grass-roots movement together of manufacturing presidents and CEOs to say to the governor and the lieutenant governor that the safety of our employees is absolutely number one,” Berg said. “We feel that we can put the protocols in place to assure their safety.”
For her own workers, Berg decided early in the pandemic that she wanted to do more than just mitigate the spread of coronavirus at the Vitamix plant. Zero tolerance was her goal, she said.
In mid-March, the company allowed remote working for corporate employees.
On March 23, Vitamix gave nearly all employees a week off with pay to prepare themselves and their families — except for a small “Tiger Team” that was charged with coming up with their own safeguards for operating safely through the virus.
In addition to instituting temperature checks, now increasingly standard at workplaces, the company set up a hotline for employees to call if they feared they were exposed to the virus during their time off.
Berg said the company realized it was important to make sure that workers felt they would be safe if they went to work.
“How do we create an environment that all the employees will easily be able to comply with following our protocols, but also have the emotional feeling of safety?” Berg said.
Even employees, like Trainer Amy Collins, whose job has changed dramatically, are getting used to a new way of doing things. Because she can’t social distance in her job, Collins can only train employees in five-minute intervals.
Some of the early measures misfired, the company admits. A first attempt to impose social distancing on the assembly line involved white opaque plastic sheeting. It prevented the spread of the virus — but it left people feeling cut off from co-workers who were only a few feet away.
It also made it impossible for workers to hear each other. The only sound from the factory floor came from machines.
“They [workers] were uncomfortable with that,” said Lisette Mendez, a team leader. “They felt like they were enclosed. They couldn’t communicate with each other.”
So the company swapped out the sheeting for plexiglass.
So far, the company’s strategy appears to be working. After initial disruptions, the plant is now operating at close to usual capacity. By May, the company said in an email, the plant was almost back to pre-coronavirus efficiency.
And workers’ fears of getting sick on the job have receded.
When the virus first reached Ohio, assembler Victoria Schade was hesitant about coming to work because she feared becoming infected in a plant with so many workers. She even took off additional days when most of the plant got off in March.
“When I came back and I walked into the building, … there’s a sign that said we need to be wearing masks,” she said. “Then I saw all these barriers, and my anxiety level wasn’t crazy anymore.”